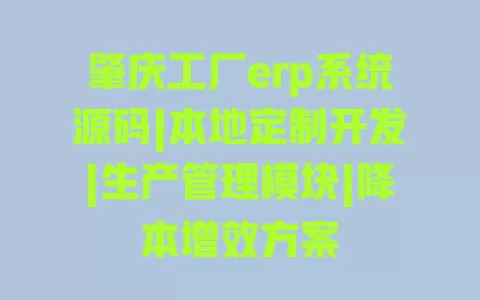
为什么肇庆工厂更需要本地定制的ERP系统源码?
去年我帮肇庆高要一家五金配件厂的朋友老周做过ERP系统改造,他之前用的是某知名品牌的通用ERP,花了20多万,结果用了半年就扔在一边了。我去厂里调研时发现,他们的生产流程很特殊:既有按订单生产的定制件,又有批量生产的标准件,通用系统的生产模块只能按一种模式排程,导致计划员每天要手动调整十几个表格,车间主任天天追着要物料,仓库管理员对着系统库存和实际货架发呆。后来我们找了本地一家有源码开发能力的团队,基于他们的生产流程定制了ERP系统,三个月后老周跟我说:“现在计划员每天下班准时走,仓库盘点差异从之前的15%降到2%,上个月电费都省了8000多——机器 idle 时间少了。”
中小工厂的“通用系统陷阱”:3个绕不开的痛点
肇庆大部分工厂都是中小规模,年产值从几百万到几千万不等,生产流程往往带着“老板经验型”特色——比如有的塑料厂老板根据天气调整注塑温度,有的五金厂有自己摸索的物料搭配比例,这些“隐性知识”很难被通用ERP系统的标准化模块覆盖。我接触过的10家肇庆工厂里,有8家提到了三个共性问题:
中国信通院《制造业数字化转型发展白皮书》里提到,2023年制造企业ERP系统实施失败案例中,“系统与实际流程不匹配”占比高达42%,其中中小厂的失败率比大厂高出18个百分点,核心原因就是“用标准化系统套个性化流程”。
源码定制的3个核心优势:比通用系统更“懂”肇庆工厂
为什么强调“源码”?举个例子,老周的工厂后来用的定制系统,源码掌握在本地开发团队手里,他们想加一个“订单优先级标记”功能——因为老客户的急单需要插队生产,开发团队当天就改好了代码,第二天就上线了,没额外收费。这就是源码的价值:你不仅买了系统,还拥有了修改它的“钥匙”。具体来说,对肇庆工厂有三个不可替代的好处:
:本地开发团队会上门驻场调研,把工厂的生产流程画成流程图,连“哪个工位的师傅习惯用纸质工单签字”这种细节都考虑到。比如肇庆大旺的电子厂,插件、焊接、组装是三个独立车间,物料需要跨车间转运,定制系统就专门开发了“跨车间物料调拨预警”,前道车间备料完成后自动提醒后道车间接收,避免物料堆积在过道。
:没有源码的话,系统升级、功能修改都要依赖原厂,按“人天”收费(市场价2000-3000元/人天)。有了源码,本地团队熟悉代码结构,改一个功能可能只需要1-2天,成本不到原厂的三分之一。去年帮老周的工厂加“生产异常上报”模块(比如机器故障、物料不合格时,车间员工扫码就能提交,管理人员实时收到通知),本地团队只收了5000元,而原厂报价3万。
:通用系统的数据存在厂商的云端,工厂担心核心生产数据(比如成本构成、客户订单)泄露。定制源码系统可以部署在工厂自己的服务器上,数据存储、备份都由自己掌控。肇庆鼎湖一家模具厂就因为这个原因放弃了云端ERP,他们的模具设计图纸属于核心机密,用本地源码系统后,IT负责人每周亲自备份数据,安全感直接拉满。
怎么判断源码定制是否“靠谱”?3个验证方法
你可能会担心:“源码定制听起来好,但怎么避免被开发团队坑?”分享三个老周当时用过的方法,亲测有效:
生产管理模块:从“头痛医头”到“系统降本”的核心抓手
老周的工厂用定制ERP后,最明显的变化在生产管理环节——之前他每天到厂第一件事是听各部门汇报问题:“张师傅的机床缺料了”“这批订单的合格率只有85%”“仓库里的A物料又积压了500公斤”。现在打开系统后台,生产数据大屏上实时显示:“当前生产订单12个,3个已完工,6个正常进行,3个预警(其中2个缺料,1个工序超时)”,问题一目了然,他每天只需要花30分钟处理预警项,剩下的时间可以去跑客户。
生产管理模块的4个“降本增效开关”
定制ERP的生产管理模块不是简单地把纸质流程搬到线上,而是通过数据联动和规则设定,帮工厂“自动省钱”。以老周的五金厂为例,这四个功能让他们半年省下了30多万:
通用系统的排产往往是“一刀切”,按订单先后顺序排,不考虑设备负荷和工人技能。定制系统可以根据工厂实际情况设置规则,比如:“优先安排交期紧急的订单”“同一台设备连续生产相似产品减少换模时间”“熟练工优先操作复杂工序”。老周的工厂有3台数控车床,之前经常出现“这台机器忙到加班,那台闲半天”的情况,用了智能排产后,设备利用率从65%提到了82%,每月多生产800多件产品,人工加班时间减少40%。
很多工厂的物料管理还停留在“经验采购”——仓库管理员看快没了就申购,结果要么生产时缺料停产,要么买多了堆在仓库占资金。定制系统的MRP模块会根据生产订单、BOM清单(物料清单)和现有库存自动算需求:比如接到1000件产品订单,系统会拆分成“需要A物料2000个、B物料500个”,再减去当前库存1200个A、300个B,自动生成“申购A物料800个、B物料200个”的采购单,还会考虑供应商的交货周期,避免临时加急采购多付运费。老周的工厂之前A物料库存周转天数是45天,现在压缩到28天,库存资金占用减少了25万元。
车间员工用手机扫码报工(比如“完成第3道工序,合格10件,返工2件”),数据实时同步到系统,质检人员扫码录入质检结果,形成“生产-质检”闭环。之前老周的工厂出现过“客户投诉产品尺寸不合格”,查了半天不知道是哪个工序出的问题,现在系统能追溯到“3月15日14:00,李师傅操作的第5台机床,因为刀具磨损导致尺寸偏差”,直接找到责任人并调整设备维护计划,产品合格率从88%提到了95%,返工成本每月省1.2万元。
很多工厂的电费、水费是“糊涂账”,不知道哪台设备、哪个工序最耗电。定制系统可以对接电表、水表,实时监控各设备能耗,比如老周的工厂发现“2号压铸机的能耗是其他机器的1.5倍”,检查后发现是液压系统漏油导致压力不足、能耗增加,修好后每月电费省了6000多元。
本地工厂案例:3个月实现“人均效能+22%”的秘密
肇庆四会一家年产值2000万的汽车零部件厂,去年用定制ERP系统后,生产管理数据发生了明显变化(数据来源:工厂提供的2023年Q3-Q4对比报表):
指标 | 系统上线前(Q3) | 系统上线后(Q4) | 变化幅度 |
---|---|---|---|
人均日产量(件) | 32 | 39 | +22% |
生产周期(天) | 12 | 9 | -25% |
物料损耗率 | 8% | 5% | -37.5% |
订单交付及时率 | 75% | 92% | +17% |
厂长跟我说:“以前催生产进度要挨个车间跑,现在打开手机就能看每道工序到哪了;以前客户问‘我的订单到哪一步了’,我要让文员查半天,现在直接把系统里的进度截图发给客户,信任感一下子就上来了。”
如果你厂里也有生产计划混乱、物料管理头疼、成本降不下来的问题,不妨试试联系本地的ERP开发团队——最好是有5年以上肇庆工厂服务经验的,先让他们免费做个需求梳理,看看源码定制能不能帮你“量体裁衣”。记得按我前面说的方法验证靠谱性,试了之后欢迎回来告诉我效果,说不定你的工厂也能像老周他们一样,用系统把效率提上去,把成本降下来。
说实话,不是所有肇庆工厂都非得砸钱搞定制ERP源码,得看自家厂子的实际情况。一般来说,年产值500万以上的工厂,定制的性价比才比较高——你想啊,要是厂子规模太小,一年到头就几条生产线、几十号人,流程简单到老板自己拿个本子都能记清楚,那通用系统凑合用用也够了,没必要花那笔定制钱。但要是过了500万这个坎,生产流程往往就开始“拧麻花”了:比如肇庆常见的五金厂,接了个大客户的定制订单,要做一批带logo的异形零件,同时车间里还在批量生产标准螺母,这两种模式混在一起,通用系统的生产模块就懵了——要么只能按定制单排程,批量生产的零件堆在仓库占地方;要么按批量排,定制单的交期又赶不上。这种“定制+批量混合生产”的厂子,最适合用源码定制,能把两种模式的排程逻辑都写进去,计划员不用天天对着表格抓狂。
再具体到人数规模的话,100人以下的中小工厂,可以先从“基础版定制”入手,不用一上来就追求“大而全”。重点抓生产和库存这两个核心模块就行:生产模块解决计划排程、工序报工的问题,库存模块管好物料进出和预警,其他像财务、销售这些,可以先用简单的表格或者通用软件过渡,这样成本能控制在50-80万,压力不会太大。我去年帮端州一家80多人的塑料厂做过,他们就只定制了生产和库存模块,上线后仓库盘点时间从3天缩到1天,生产缺料的情况少了70%,老板说“这50万花得比之前20万买的通用系统值多了”。要是厂子规模到了100-300人,比如鼎湖那些电子配件厂,有好几个车间、十几条产线,那最好还是全流程定制,从采购、生产、仓库到销售、财务全打通,预算大概80-150万。这种厂子流程环节多,数据流转复杂,缺了哪个模块都可能出现“卡脖子”,比如采购和生产数据不通,就会要么多买料压资金,要么少买料停生产线,全流程定制虽然前期投入多,但后面省下来的效率成本,基本1-2年就能回本。
肇庆工厂定制ERP系统源码的成本大概是多少?
本地定制ERP系统源码的成本通常根据工厂规模、功能需求复杂度而定,一般在50-150万之间。相比通用系统(20-50万)初期投入略高,但长期节省二次开发和适配成本。例如文中提到的五金厂案例,通过定制系统半年内综合成本降低18%,1-2年即可回本。
本地定制ERP系统的开发周期需要多久?
标准开发周期为3-6个月,包含需求调研(2-4周)、源码开发(8-12周)、测试优化(4-6周)和员工培训(2-3周)。像文中老周的五金厂,因流程相对简单,3个月即完成上线;若涉及复杂生产模块(如多车间联动、设备物联网对接),周期可能延长至5-6个月。
有了ERP系统源码,工厂自己能进行二次开发吗?
可以。正规定制服务会提供完整源码授权书,工厂拥有永久使用权和二次开发权。但 初期由本地开发团队完成核心功能,后续简单调整(如增加报表字段、修改审批流程)可由工厂IT人员操作。例如文中提到的“订单优先级标记”功能,本地团队当天即可完成源码修改,工厂后期若有基础编程人员,也可自主调整。
哪些规模的肇庆工厂适合定制ERP系统源码?
年产值500万以上、生产流程有明显特殊性的工厂更适合。尤其是像肇庆本地常见的“定制+批量混合生产”模式(如五金、塑料、电子配件厂),通用系统适配性差,定制源码能精准匹配流程。中小工厂(100人以下)可选择基础版定制(聚焦生产+库存模块),成本控制在50-80万;中型工厂(100-300人) 全流程定制,预算80-150万。
本地定制ERP系统的数据安全如何保障?
本地定制ERP支持部署在工厂自有服务器,数据存储、备份完全自主可控。开发团队会提供数据加密、权限分级(如车间员工仅能查看本工序数据)、操作日志追踪等功能,同时协助工厂建立定期备份机制(如每周手动备份+云端容灾)。正如文中鼎湖模具厂案例,通过本地部署和源码掌控,核心生产数据(如设计图纸、成本构成)无需上传第三方云端,安全风险大幅降低。